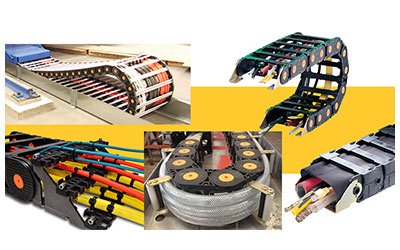
Are designing or maintaining automated moving equipment?
Design World’s December issue discusses maintenance considerations for industrial cables.
Dynatect supplies optimized cable carrier systems to keep dynamic cable packages in working order.
Cable carriers are important to dynamic cables and can also impact maintenance cycles, here’s how:
- Abrasion – Abrasion can by mitigated by the proper specification of cavity dividers, separators & cable clamps
- Oil – Lids and Hose Sleeves can enclose a carrier to either shield out contaminants or help contain hoses that spring a leak
- Torsion/Twisting – Carriers help maintain a proper bend radius and help prevent twisting when properly specified.
- Maintenance – Snap-open lids, crossbars, and easy-to-replace links make it easier to replace segments of either the carrier links or cables/hoses if damage should occur
Why do cables fail?
Cables fail for a variety of reasons. These are ranked in order from the most common problems we see.
- A low-flex cable is in use – Cables flexing in a cable carrier are subjected to both tensile and compressive forces as they both bend and roll through the radius. Cables not designed for continuous flexing may cause the outer coating/jacket to bend and break. It will also cause the conductor strands to break down and begin to “corkscrew”
- Installation error – the most common is not uncoiling the cable, or the cable is either too tight or too loose. Proper installation in conjunction with clamping cables ensure that the proper length of cable stays consistently in the carrier. Cables ideally should ride as close to the neutral axis of the carrier as possible. Cables should be laid in the carrier if possible, making certain that the cable/hoses are laid into the carrier “twist-free”. Cables/hoses supplied in rolls or on reels should be unrolled, not pulled sideways or off the top of the coil.
When stacking cables/hoses, care should be taken to ensure enough slack has been provided to allow cables/hoses to travel freely on top of one another. The stacking or direct side-by-side placement of cables and hoses with large cross-sectional differences is not recommended
- Cable clamps are not used – Cables that are not clamped can either pull against the inner radius, causing jacket and cross bar wear. Or they will pull cables into the carrier causing them to snake and bunch through cross bars at the radius. Dynatect offers a variety of clamping methods.
- Bend radius is too tight – Although 8 to 10 times the outer diameter (OD) is a rule of thumb for radius selection, many industrial grade “SO” style cables are rated at 15 times the OD.
- Carrier is undersized – When a carrier is undersized, the cables scuff against each other, the sidebands, cross bars, and dividers. Eventually, the outer jackets will wear through. Steel braided cables and hoses will saw through cross bars as the jackets wear.
- Cross bar material/design – Plastic cross bars are not always the best choice for cable wear. Friction is generated when plastic jackets rub on plastic bars. Flat aluminum bars offer an excellent wear medium against plastic jacketed cables. Thin/narrow aluminum bars can cause point wear. Poly rollers provide a low friction, mechanical wear surface.
- Cavity separators are not used – When cables and hoses are installed without separators, they will cross and twist over time. In high velocity and long travel applications, this twisting can occur very rapidly, causing the cables to snake and “corkscrew”. Effective separation ensures that when multiple cables are in 1 compartment, that the compartment height is not large enough to allow them to cross. Separation can help ensure that the cables ride the neutral axis of the carrier.
For more about clamping, installation, or sizing a cable carrier, visit these links or Find a Rep today: