Rubber Molding Processes
Ro-Lab has several processes available to produce the ideal rubber part for your application.
- Rubber Compression Molding: Rubber compression molding is the most widely used production method for rubber molding and the simplest method used for the production of elastomeric materials. In this process, material is placed directly into the cavity of the mold. Pressure is applied which forces the material to conform to the cavity shape. The cure occurs as the pressure and heat cause the thermoset material to crosslink. For the ability to meet close tolerances, compression molding is the preferred process for gaskets, seals and o-rings.Ro-Lab’s 1,400 ton compression press is ideal for large molds, or thin sheets with close tolerances. There is ample capacity for production of large-scale parts; as well as smaller, high volume runs. Multi-cavity molds can produce tiny parts down to two grams. Our equipment allows for continuous curing for long, uninterrupted items.
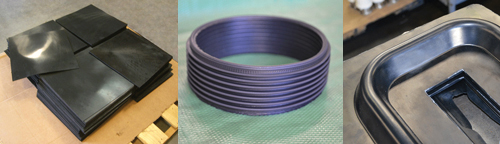
- Rubber Injection Molding: This process most commonly injects preheated thermoplastic or thermosetting polymers directly into a mold. It is capable of molding parts more intricate than both transfer and compression molding. The advantages of injection molding: – Delivers faster curing times than compression or transfer molding – Shortens cycle times – Ideal for high volume component production Compared to compression molding, injection molding is a more complex process that injects a preheated material into the cavities of a closed mold.
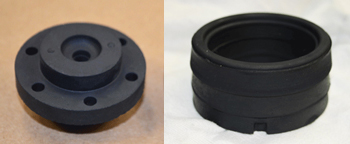
- Rubber Transfer Molding: In a process that is a hybrid of compression and injection techniques, a piston forces preheated material from a transfer pot into a closed mold. Transfer molding advantages include: increased productivity, product quality and product consistency. Molding with inserts is possible where either a metal or ceramic insert is placed into the cavity prior to injection and the heated plastic bonds to the insert during rubber molding process. This process is capable of molding part shapes that are more intricate than compression molding. This is because transfer molding uses a closed mold and can therefore achieve tighter tolerances. It produces a good surface finish and has dimensional stability.In summary, the benefits of rubber transfer molding are:
- Finished components with intricate shapes
- Compatible with the use of delicate insets
- Delivers tight dimensions and tolerances
- Usable for all rubber durometers
- Special Rubber Processes: Ro-Lab produces hoses, rolls, lined pipes, and other mandrel-made products.

- Hoses are hand built on a mandrel (cylindrical form) in a variety of configurations:
- Soft or wire reinforced walls
- Plain ends, or duck and rubber flanges with back-up rings
- Built-in nipples
- Other Mandrel-made products:
- Non-hose mandrel-made products with 4” – 60” diameters with lengths to 50’
- Rubber transition chutes
- Mandrel-made endless belts
- Industrial and agricultural rolls:
- Rubber or urethane covers
- New or stripped/recovered cores
- Roll regrinding
- Crowns and grooves
- Rubber-lined pipes for mining, oil and gas
Rubber 101
Rubber Basics – There are two types of rubber, natural and synthetic. Natural rubber is an elastic polymeric substance made from latex of a tropical plant and synthetic rubber is produced from the polymerization of oil byproducts. Rubber whether natural or synthetic, is a great alternative to plastic and metal for applications that require a more elastic solution. Rubber also has waterproof, electrical insulating and tearing resistant properties. Some types of rubber are resistant to oils, solvents and other chemicals.
Durometer (hardness) – Depending on the type of rubber the hardness will range from Shore A (softer) to Shore D (harder) to Shore 00 (foam/sponge). Rubber products range from sponges and erasers to bowling balls and tires.
Tensile & Tear Strength – The tensile (tension) and tear strength of rubber will vary based on the type of rubber. For the most part, rubber in general has a fair to excellent tear and tensile strength. Therefore it is important to select the proper rubber type that best fits your application.
Advantages |
Varied Resistances Levels |
Elasticity |
Abrasion |
Resilience |
Impact |
Hardness Flexibility |
Shearing/Tearing |
Tensile & Tear Strength Flexibility |
Atmospheric (Oxygen/Ozone/UV) |
Machinability |
Temperature |
Noise Reduction |
Water |
Vibration Reduction |
Chemicals |
Compare Properties
Property |
Polyurethane |
Nitrile Rubber |
Neoprene Rubber |
Natural Rubber |
SBR |
Butyl |
Tensile Strength (MPa) |
20.7 to 65.5 |
13.8+/- |
20.7+/- |
20.7+/- |
18.8+/- |
18.8+/- |
Durometer |
5A to 85D |
40 to 95A |
40 to 95A |
30 to 90A |
40 to 90A |
40 to 75A |
Specific Gravity |
1.10 to 1.24 |
1.0 |
1.23 |
0.93 |
0.94 |
0.92 |
Tear Resistance |
Outstanding |
Fair |
Good |
Good |
Fair |
Good |
Abrasion Resistance |
Outstanding |
Good |
Excellent |
Excellent |
Good-Excellent |
Good |
Compression Set |
Good |
Good |
Fair-Good |
Good |
Good |
Fair |
Rebound |
Very High to Very Low |
Medium |
High |
Very High |
Medium |
Very Low |
Gas Permeability |
Fair-Good |
Fair |
Low |
Fair |
Fair |
Very Low |
Acid Resistance |
Fair-Good |
Good |
Excellent |
Fair-Good |
Fair-Good |
Excellent |
Aliphatic Hydrocarbons |
Excellent |
Excellent |
Good |
Poor |
Poor |
Poor |
Aromatic Hydrocarbons |
Fair-Good |
Good |
Fair |
Poor |
Poor |
Poor |
Oil and Gas Resistance |
Excellent |
Excellent |
Good |
Poor |
Poor |
Poor |
Oxidation Resistance |
Outstanding |
Good |
Excellent |
Good |
Good |
Excellent |
Ozone Resistance |
Outstanding |
Fair |
Excellent |
Fair |
Fair |
Excellent |
Low Temperature Resistance |
Excellent |
Good |
Good |
Excellent |
Excellent |
Good |
Durometer (Hardness) Scales
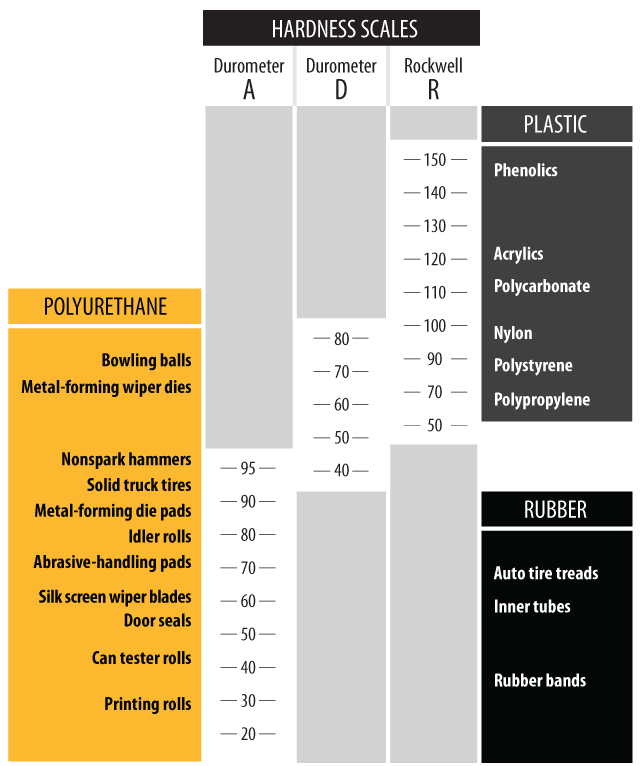